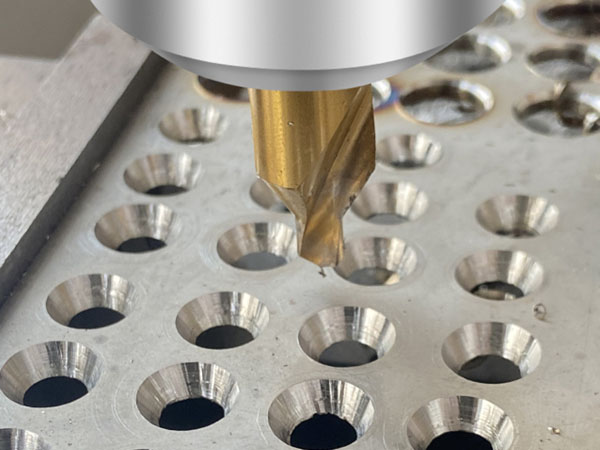
The proper selection and use of center drills are essential for achieving precision and efficiency in machining. Below are key considerations when using center drills:
Choosing the Correct Drill Angle:
The choice of drill angle should depend on the material of the workpiece and the specific machining operation. For most materials, a 60° taper angle is standard, while harder materials may require an R-type center drill with a curved cutting edge.
Controlling Drilling Speed:
The drilling speed should be carefully controlled to avoid overheating and wear. Excessive speed can cause tool overheating and dulling, while too low a speed may reduce machining efficiency. The appropriate speed should be determined based on the material hardness, drill diameter, and machine tool capacity.
Cooling and Lubrication:
Proper cooling and lubrication during drilling help reduce tool wear and enhance the surface finish of the workpiece. The use of cutting fluids helps dissipate heat generated during friction and prevents tool and workpiece deformation due to excessive heat.
Inspecting Tool Wear Regularly:
After extended use, the cutting edges of center drills may become dull or worn. Regular inspection is important, and worn tools should be replaced or sharpened in time to maintain machining accuracy.
Methods for Drilling Center Holes
Drilling a precise center hole is the first step in machining, and the quality of this hole directly affects the overall precision of the process. Here are key methods and techniques for drilling center holes:
Securing the Workpiece:
Before drilling, the workpiece must be securely clamped to the machine. Any movement or misalignment will result in deviations in the center hole, negatively impacting subsequent machining.
Selecting the Appropriate Center Drill:
Depending on the material, required hole diameter, and the subsequent operations, the correct type and size of center drill should be selected. For long workpieces or those requiring deep machining, a Type C center drill is recommended.
Drilling Steps
Start the drilling process at a low speed to slowly guide the center drill into the workpiece and ensure accurate positioning.
Gradually increase the speed to the appropriate rate, maintaining a steady drilling process until the center hole reaches the desired depth.
When stopping, lift the tool smoothly to avoid damaging the workpiece surface.
Re-drilling or Secondary Calibration
For high-precision workpieces or those requiring multiple machining steps, secondary calibration or re-drilling may be necessary. After the initial hole is drilled, a larger diameter center drill may be used to achieve better concentricity and accuracy.
Using Auxiliary Tools
In some high-precision applications, CNC machines can be used to automate the positioning and drilling process, further improving efficiency and accuracy.
Center drills and the proper creation of center holes play an essential role in the field of machining. By selecting the correct type of center drill, controlling machining conditions, and ensuring a good match between center hole and tip angles, precision and efficiency can be significantly improved. The various shapes and functions of center drills provide versatile and reliable solutions for a wide range of machining needs, making them indispensable tools in modern manufacturing.
OEM Capability

Categories
HSS-PM Taps | HSSE-M42 Taps |
HSSE / HSS Taps | Spiral Flute Taps |
Straight Flute Taps | Spiral Point Taps |
Multi-function Taps |
Solid Carbide Drill Bits | Twist Drill Bits |
Center Drill Bits | Indexable U Drills |
Flat-end Milling Cutter | Ball Nose End Mills |