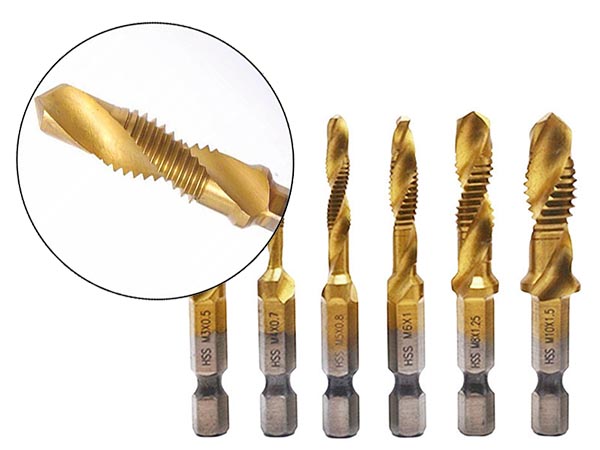
How to Choose Tap Tolerance Grades: A Practical Guide for DIY and Factory Use
In a repair shop tucked away in a Zhejiang auto parts market, veteran mechanic Li Ming noticed a persistent issue—freshly replaced cylinder head bolts kept coming loose. After meticulous inspection, he traced the root cause: the commonly used H5-grade taps had produced oversized thread clearances in aluminum alloy parts. This costly mistake—amounting to 3,800 yuan—highlights a critical yet often overlooked truth: tap tolerance grades aren't just performance stats, they're material mechanics equations in disguise. Whether you're running a home workshop or managing an industrial production line, choosing the wrong tap grade can lead to anything from minor part failures to major system breakdowns. This article unpacks the real logic behind tap grade selection—and reveals the survival strategies manuals never tell you.
Tolerance Grades Are IDs, Not Test Scores
(Understanding Three Key Parameters)
The ISO-standard H1 to H6 grades are like phone models—Pro, Max, SE—each alphanumeric combo maps to a set of practical characteristics:
1. Tolerance Range (Permissible Dimensional Error):
- H1: ±0.005 mm (1/15 of a hair’s width)
- H3: ±0.01 mm (about the thickness of copy paper)
- H5: ±0.03 mm (like A4 paper thickness)
Examples:
- M1.6 screws for smartphones → H1
- M6 screws for furniture assembly → H3
2. Thread Surface Finish:
- DIY-grade: Minor tool marks visible (like a carrot sliced with a kitchen knife)
- Industrial-grade: Mirror finish (like the inside of a stainless steel thermos)
3. Service Life:
- Basic grade: 100 holes (roughly the lifespan of 500 phone charges)
- Reinforced grade: 3,000 holes (comparable to military-grade rugged phones)
The Hidden Parameters Behind Tolerance Grades
1. Temperature Sensitivity Coefficient:
- H1: Dimensional variation ≤0.001 mm per 10°C rise (ideal for precision labs)
- H5: Variation of 0.005 mm per 1°C shift (risky for outdoor work)
2. Material Compatibility “Secret Code”:
Workpiece Material | Recommended Grade | Coating Type | Warning Sign |
---|---|---|---|
304 Stainless Steel | H2 | TiAlN | Orange peel-like surface on threads |
Aluminum Alloy | H3 | Uncoated | Chips stick in flutes |
Titanium Alloy | H1 | AlCrN | Blue discoloration on tap tip |
3. Tapping Speed Reference Table:
Grade | RPM (Steel) | Coolant | Noise Alert |
---|---|---|---|
H1 | 50–100 rpm | Fully synthetic cutting oil | >75 dB indicates abnormality |
H3 | 150–300 rpm | Water-based emulsion | >85 dB needs inspection |
H5 | 500+ rpm | Dry or minimal lubrication | 90 dB short bursts acceptable |
Five Real-World Tapping Fails
- The Home Renovator’s Blunder Used H5 taps for bathroom hardware—loose screws in 3 months due to poor thread engagement.
- The Model Hobbyist’s Lesson Used H1 taps on RC car metal parts—broke the tap; ultra-precision tools can’t always survive manual use.
- Hardware Store Complaint Farmer returned H3 tap for being "unreliable"—should’ve used a mid-grade reinforced tap for machinery.
- Small Factory’s Quality Crisis 1% defect rate in mass-produced phone parts—caused by not recalibrating H2 taps every 200 holes.
- Auto Repair’s Hidden Cost Tried saving 10 yuan by buying lower-precision taps—ended up spending 2 hours redoing a gearbox repair.
Foolproof 3-Step Selection Method
Step 1: Match the Use Case
Scenario | Grade | Price Range | Service Life |
---|---|---|---|
Home DIY | H4–H5 | ¥5–15 | ~50 uses |
Auto/Farm Repairs | H3 | ¥20–50 | ~200 uses |
Smartphone/Watch Repairs | H1–H2 | ¥80–150 | ~100 uses |
Mass Production | H2–H3 | Custom pricing | ~3,000 uses |
Step 2: Feel It Out (In-Store Tips)
- Good Tap: Smooth turn when tested on scrap metal, no jerky movement
- Bad Tap: "Clunk" noises, crumbly chips, or burrs on threads
Step 3: Check Anti-Counterfeit Labels
- Laser-etched "H" + number (not paint-stamped)
- Traceable QR code on packaging
- Test report with at least three diameter measurements
Industry Insider Benchmarks
- Automotive Industry Acceptance Criteria:
- Volkswagen TS-654312: Thread mid-diameter fluctuation ≤0.008 mm across 1,000 holes
- Toyota ADV-2023: 5% of each tap batch must pass metallographic inspection
- Smart Device Component Standards:
- Apple supply chain: M1.4 or smaller threads require H0.5 taps (non-standard grade)
- Huawei supplier entry: Tapping axial force variation <15% (requires intelligent tap holders)
- Defense & Aerospace Requirements:
- Submarine-grade taps: 72-hour salt spray resistance (vs. 24-hour standard)
- Aerospace taps: Maintain ±0.003 mm precision in vacuum environments
Advanced Users: Troubleshooting Guide
1. Threads Feel Like Sandpaper
- Likely cause: Incorrect rake angle for material
- Fix: Use 10–12° rake for stainless steel
2. Frequent Tap Breakage
- Check in order: Hole diameter → Cutting speed → Cooling → Fixture rigidity
- Quick fix: Add WD-40 at hole entry
3. Inconsistent Thread Dimensions
- Red flag: Hole diameter deviation >0.015 mm—stop use immediately
- Calibration: Use three-point thread gauge for daily checks
Old-School Maintenance Tricks
Even with the right grade, misuse can ruin a tap. Veteran techs swear by these:
- Before tapping: Apply toothpaste (DIY cutting paste)
- For cast iron: Back out ¼ turn every ½ rotation
- For stuck taps: Soak in cola for 30 minutes (acid dissolves chips)
- For storage: Use desiccants from heat packs to prevent rust
Final Thoughts:
Tap tolerance grades are not just numbers—they’re precise translations of manufacturing context. H1 to H6 codes embody the complex interplay of material traits, machining parameters, and cost controls. A car repair shop doesn't need aerospace precision, just like a medical device manufacturer can't settle for construction-grade tolerance. As intelligent taps and 3D printing evolve, this precision game is entering the microscopic domain. Remember: the key to a perfect thread isn’t the tap’s price tag, but its resonance with the machining environment. When temperature, spindle speed, and material align in a golden triangle, true thread quality takes shape.
OEM Capability

Categories
HSS-PM Taps | HSSE-M42 Taps |
HSSE / HSS Taps | Spiral Flute Taps |
Straight Flute Taps | Spiral Point Taps |
Multi-function Taps |
Solid Carbide Drill Bits | Twist Drill Bits |
Center Drill Bits | Indexable U Drills |
Flat-end Milling Cutter | Ball Nose End Mills |