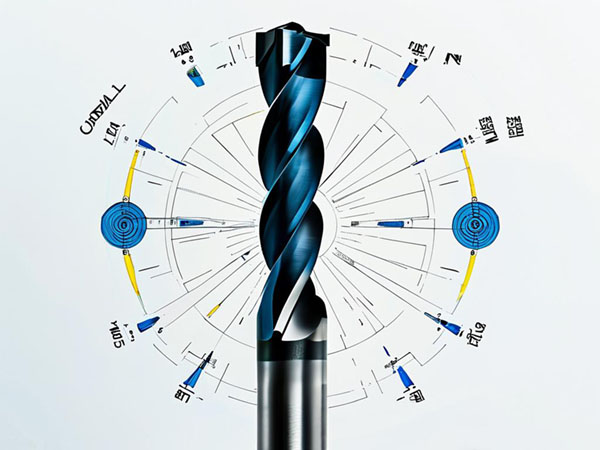
How to Design Milling Cutter Geometry Parameters (Helix Angle, Number of Flutes, and Slot Type)
1. The Key Role of Geometry Parameters (Helix Angle, Number of Flutes, Slot Type) in Milling Cutter Design and Performance
Milling cutter geometry parameters, including the helix angle, number of flutes, and slot type, are crucial factors influencing the cutter's performance. A well-designed cutter geometry can significantly improve cutting efficiency, machining accuracy, and tool life. These parameters affect not only cutting forces but also chip removal, cutting temperature, vibration, and surface quality. Therefore, they play a vital role in the overall design of milling cutters.
2. Comprehensive Consideration of Helix Angle, Number of Flutes, and Slot Type
2.1 Coordination and Interaction of Different Geometry Parameters
The helix angle, number of flutes, and slot type of a milling cutter interact and depend on each other. These parameters must be considered in a balanced way during the design process. For example, increasing the number of flutes can enhance cutting efficiency but may increase cutting forces and vibration, requiring adjustments to the helix angle and slot type to maintain balance. A larger helix angle reduces cutting forces but may increase tool load, necessitating optimization based on the specific needs of the process.
2.2 Optimized Design Methods for Milling Cutter Geometry Parameters
- How to Balance Helix Angle, Number of Flutes, and Slot Type
Balancing these three geometry parameters depends on understanding the specific machining requirements. In high-feed and deep-cut machining, a smaller helix angle and larger number of flutes are beneficial for efficiency. For precision machining, a larger helix angle can help reduce cutting forces and improve surface quality.
- Comprehensive Consideration of Cutting Forces, Machining Accuracy, and Tool Life
Optimized design must take into account cutting forces, machining accuracy, and tool life. Increasing the number of flutes and decreasing the helix angle can improve efficiency but also lead to higher cutting forces. A suitable slot type can reduce force concentration, improving tool life and accuracy.
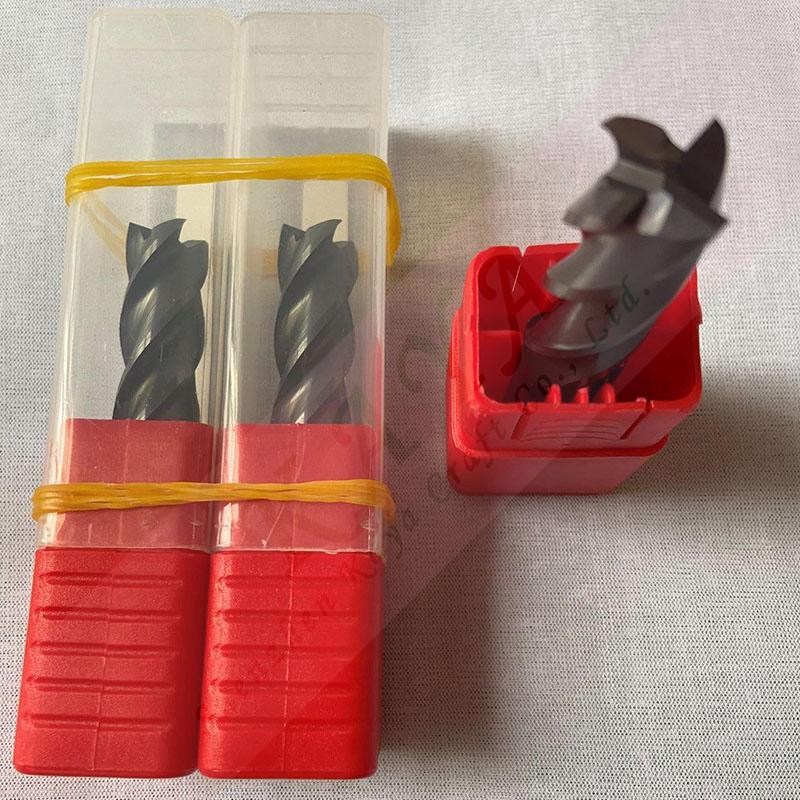
2.3 Geometry Parameter Adjustments in Design Practice
In practical design, milling cutter geometry parameters often need to be adjusted according to specific machining requirements. For different materials and processes, varying helix angles and numbers of flutes may be employed. For hard materials, smaller helix angles and more flutes are often used; for softer materials, a larger helix angle may enhance cutting efficiency and tool life.
2.4 Geometry Parameter Selection for Different Materials
- Differences in Milling Cutter Design for Rigid vs. Ductile Materials
Rigid materials such as steel and cast iron require higher cutting forces and larger helix angles for stable cutting. Ductile materials such as aluminum and copper alloys, with lower cutting forces, typically use larger numbers of flutes and smaller helix angles to improve efficiency.
- Processing Requirements for High-Temperature Alloys and Hardened Steel
High-temperature alloys and hardened steels generate high cutting temperatures, accelerating tool wear. To reduce cutting forces and manage cutting temperatures, larger helix angles and appropriate slot types should be chosen to alleviate heat buildup and extend tool life.
2.5 Matching Geometry Parameters with Machine Tool and Process Conditions
- Compatibility Between Machine Rigidity, Power System, and Tool Geometry Parameters
The rigidity and power system of the machine tool play a significant role in selecting milling cutter geometry. For low-rigidity machines, smaller helix angles and fewer flutes can reduce tool load and improve stability. Conversely, high-rigidity machines may accommodate larger helix angles and more flutes to increase cutting efficiency.
- The Impact of Cutting Speed and Feed Rate on Geometry Parameter Selection
Cutting speed and feed rate influence the selection of geometry parameters. At high cutting speeds, smaller helix angles help reduce heat buildup, preventing premature tool wear. At higher feed rates, more flutes help evenly distribute cutting forces, minimizing vibration.
3. Practical Applications of Milling Cutter Geometry Parameters
3.1 Selection of Geometry Parameters for Different Machining Scenarios
- Roughing vs. Finishing
In roughing operations, milling cutters need to withstand higher cutting forces, so larger numbers of flutes and smaller helix angles are often used. For finishing operations, smaller numbers of flutes and larger helix angles are preferred to reduce cutting forces and improve surface quality.
- High-Speed Cutting vs. Low-Speed Cutting
High-speed cutting requires high cutting efficiency and tool stability, often calling for milling cutters with more flutes and smaller helix angles. Low-speed cutting, on the other hand, relies more on larger helix angles to control cutting forces and improve surface finish.
3.2 The Impact of Geometry Parameters on Cutting Forces and Surface Quality
Milling cutter geometry parameters directly influence cutting forces and surface quality. More flutes improve cutting capacity but may increase cutting forces and compromise surface quality. Therefore, a balance must be struck between cutting forces and surface finish, selecting appropriate helix angles and slot types.
3.3 Optimizing Geometry Parameters for Efficient Cutting
Efficient cutting demands high cutting efficiency and low cutting forces. In such cases, geometry optimization is essential. For high-feed and deep-cut operations, smaller helix angles and more flutes are often preferred to enhance efficiency and avoid overloading the tool.
3.4 The Relationship Between Tool Geometry Optimization and Production Costs
Rational milling cutter geometry design not only improves production efficiency but also reduces production costs. By minimizing tool change time, improving tool durability, and reducing tool consumption, the optimization of geometry parameters helps lower overall production costs.
4. Cutting-Edge Research and Technological Developments in Milling Cutter Geometry Parameters
4.1 The Impact of New Materials and Coating Technologies on Geometry Parameter Design
As new materials and coating technologies advance, milling cutter geometry design is also evolving. For example, nanocoatings and ultra-hard coatings improve tool wear resistance and heat resistance, leading to more versatile geometry designs.
4.2 Intelligent Manufacturing and Automatic Optimization of Milling Cutter Geometry Parameters
The development of intelligent manufacturing technologies enables dynamic optimization of milling cutter geometry based on real-time machining data. Through advanced sensors and artificial intelligence algorithms, cutter geometry can be automatically adjusted to enhance machining efficiency and quality.
4.3 The Enhancement of Milling Cutter Performance Through Nanotechnology and Microstructural Surface Treatment
Nanotechnology and microstructural surface treatments are becoming key research topics in milling cutter geometry design. These technologies can significantly improve tool performance by enhancing wear resistance, reducing friction, and improving thermal stability, thereby providing new avenues for geometry optimization.
4.4 Future Research Directions in Milling Cutter Geometry Parameter Design
Future milling cutter geometry parameter design will focus on greater efficiency, precision, and sustainability. With advancements in material science, manufacturing technologies, and intelligent systems, geometry design will evolve towards multi-condition adaptability and self-optimization to meet more complex and high-precision machining requirements.
This article outlines how to design milling cutter geometry parameters, focusing on helix angle, number of flutes, and slot type. By understanding and optimizing these parameters, milling cutter performance can be significantly improved in terms of cutting efficiency, machining accuracy, and tool life.
OEM Capability

Categories
HSS-PM Taps | HSSE-M42 Taps |
HSSE / HSS Taps | Spiral Flute Taps |
Straight Flute Taps | Spiral Point Taps |
Multi-function Taps |
Solid Carbide Drill Bits | Twist Drill Bits |
Center Drill Bits | Indexable U Drills |
Flat-end Milling Cutter | Ball Nose End Mills |