
The Application of Powder Metallurgy Technology in Drill Bit Manufacturing
In the field of hardware cutting tool manufacturing, powder metallurgy technology is gradually emerging as a key process for enhancing drill bit performance. Compared to traditional manufacturing methods, powder metallurgy allows for precise control over material structure, resulting in drill bits with superior hardness, wear resistance, and extended service life. This is particularly beneficial for machining difficult-to-cut materials such as stainless steel and hardened steel. This article provides an in-depth analysis of the advantages, core processes, and practical applications of powder metallurgy in drill bit manufacturing, helping users select more efficient cutting tools.
1. What is Powder Metallurgy Technology?
Powder metallurgy is a process that involves pressing and sintering metal powders to create high-precision components. Compared to traditional casting or forging, powder metallurgy offers better control over material composition and structure, thereby improving product performance.
Applications in Drill Bit Manufacturing:
- Suitable for HSS (High-Speed Steel), HSSE (Cobalt-Alloyed High-Speed Steel), and carbide drill bits
- Enhances drill bit hardness, wear resistance, and toughness
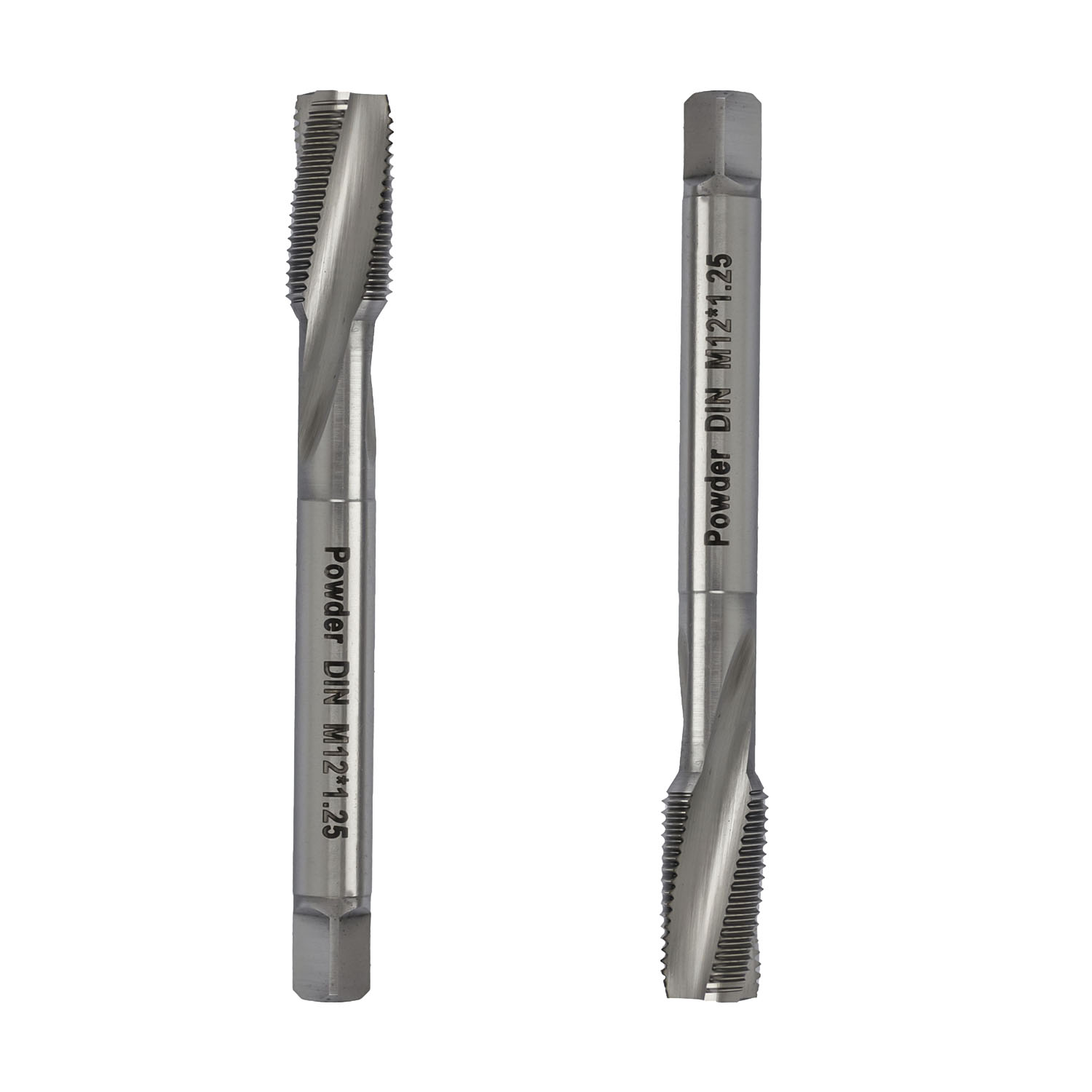
2. Core Advantages of Powder Metallurgy Technology
2.1 Comparison with Traditional Manufacturing Processes
Process Parameter | Traditional Casting | Powder Metallurgy |
---|---|---|
Carbide Size | 20-50μm | 2-10μm |
Hardness Uniformity | ±2HRC fluctuation | ±0.5HRC precision |
Material Utilization | 60-70% | Over 95% |
Minimum Production Batch | 5,000 pieces | 200 pieces (customizable) |
2.2 Key Breakthroughs in Microstructure
- Carbide Control Technology: Powder produced via nitrogen atomization achieves:
- Carbide size reduced to 1/5 of traditional methods
- Uniformity improved by 300%
- Innovative Pore Structure Applications:
- Controlled porosity of 0.5-2% for oil storage
- Self-lubricating drill bits increase tool life by 40% in aluminum alloy machining
3. Three Technical Approaches to Enhancing Drill Bit Performance
3.1 Material Formulation Optimization (Emphasizing Export Market Needs)
- For the European Market:
- HSSE-PM (8% Cobalt Content): Complies with DIN standards
- Addition of 0.3% Rare Earth Elements: Enhances high-temperature strength
- For the North American Market:
- Carbide Drill Bits with Gradient Structure:
- Cutting Edge: WC-10%Co (High Hardness)
- Transition Layer: WC-13%Co (Impact Resistance)
- Drill Body: WC-15%Co (High Toughness)
- Carbide Drill Bits with Gradient Structure:
3.2 Innovations in Sintering Processes
- Segmented Sintering Control:
- Low-Temperature Phase (800°C): 2-hour degreasing
- Mid-Temperature Phase (1150°C): 1-hour pre-sintering
- High-Temperature Phase (1280°C): 3-hour final sintering
- Post-Treatment Processes:
- Cryogenic Treatment (-196°C Liquid Nitrogen): Converts over 95% of retained austenite
- Triple Tempering: Stabilizes hardness at 65±1HRC
3.3 Coating Synergy
Machining Scenario Preferred Coating Synergistic Coating Combination Advantages High-Hardness Steel Cutting TiAlN TiAlN + TiSiN Improves high-temperature oxidation resistance by 20% Aluminum Alloy Finishing DLC DLC + Nano-Diamond Reduces built-up edge, achieves surface roughness Ra < 0.2μm Dry Cutting (No Coolant) AlCrN AlCrN + MoS₂ Reduces friction coefficient by 35% Composite Material Drilling ZrN ZrN + Alternating Nano-Multilayer Prevents adhesion, extends tool life 3× 4. Advantages of Powder Metallurgy Drill Bits
Compared to conventional manufacturing methods, powder metallurgy drill bits offer the following key benefits:
(1) More Uniform Material Structure
- Traditional cast drill bits may suffer from uneven carbide distribution, affecting cutting performance.
- Powder metallurgy technology refines carbide particles and ensures uniform distribution, enhancing wear resistance.
(2) Higher Hardness and Toughness
- By adjusting powder composition (e.g., increasing cobalt content), powder metallurgy drill bits achieve better red hardness (ability to
- maintain hardness at high temperatures).
- Ideal for machining difficult-to-cut materials such as stainless steel and hardened steel.
(3) Longer Service Life
- Powder metallurgy drill bits exhibit slower wear rates, reducing tool replacement frequency and improving machining efficiency.
- Test data shows that HSSE drill bits made with powder metallurgy last 50%-100% longer than standard drill bits.
5. Case Studies
5.1 Automotive Component Machining
German Transmission Housing Project:
- Material: EN-GJS-600-3 Ductile Iron
- Original Drill Bit: Standard carbide drill bit (80 holes per tool)
- After Switching to Powder Metallurgy Drill Bits:
- Tool life increased to 220 holes
- Per-hole cost reduced by 58%
5.2 Breakthroughs in Aerospace Applications
Titanium Alloy Machining Solution:
- Base Material: Ultra-fine grain WC-6%Co
- Composite Coating: AlTiN + MoS₂ Solid Lubricant
- Results Achieved:
- Cutting speed of 45 m/min (vs. 25 m/min for traditional drill bits)
- No built-up edge formation
6. Quality Control System
Comprehensive Inspection Procedures
- Powder Testing:
- Particle size distribution (Laser Diffraction Method)
- Oxygen content < 800 ppm
- Post-Sintering Inspection:
- Density ≥ 99.5% of theoretical density
- Porosity (Class A) ≤ 0.1%
- Finished Product Testing:
- Dynamic Rigidity Test (Simulating Cutting Force Impact)
- Cutting Performance Test (Following ISO 10899 Standards)
7. Conclusion
Powder metallurgy technology significantly enhances drill bit cutting performance and longevity through optimized material formulations, advanced sintering techniques, and intelligent coating combinations. For hardware cutting tool companies targeting international markets, adopting powder metallurgy drill bits not only meets global demands for high-precision, durable tools but also reduces customer machining costs and improves product competitiveness. Looking ahead, as new materials and smart manufacturing techniques continue to evolve, powder metallurgy drill bits will play an increasingly vital role in various industrial applications.
OEM Capability

Categories
HSS-PM Taps | HSSE-M42 Taps |
HSSE / HSS Taps | Spiral Flute Taps |
Straight Flute Taps | Spiral Point Taps |
Multi-function Taps |
Solid Carbide Drill Bits | Twist Drill Bits |
Center Drill Bits | Indexable U Drills |
Flat-end Milling Cutter | Ball Nose End Mills |