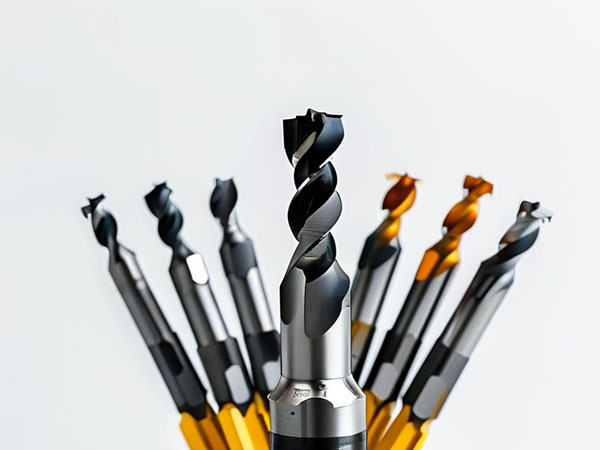
1. Definition and Types of Cutting Edges (Single, Double, and Multi-Edge)
The number of cutting edges refers to the total number of active cutting surfaces on a milling cutter that engage with the workpiece during the machining process. The number of edges plays a crucial role in determining the cutter’s performance, including cutting efficiency, tool life, and surface finish.
Milling cutters can be classified based on the number of cutting edges into the following types:
Single-edge cutters: These cutters have only one active cutting edge. They are used for specialized operations or in cases where only minimal material removal is needed.
Double-edge cutters: These cutters have two cutting edges and are commonly used for light-duty cutting, offering a balance between cutting force and surface finish.
Multi-edge cutters: These have more than two cutting edges and are typically used for high-efficiency machining in mass production. The most common multi-edge cutters are four, six, or more edges, depending on the tool’s design and application.
Each type of cutter is selected based on the specific requirements of the machining operation, such as the material to be cut, the type of operation, and the desired surface finish.
2. Measurement Standards and Techniques for Cutting Edges
The measurement of cutting edges primarily focuses on the number of active cutting surfaces, but also considers the tool's geometry, such as the cutting edge angle and the distribution of cutting edges. Modern CNC machines and tool measurement systems often include built-in functions to measure tool dimensions, including the number of edges, automatically during setup.
Techniques used to verify the number of cutting edges include:
Visual inspection: for tools with clear and distinguishable cutting edges.
Contact probes: used on CNC machines to confirm edge geometry and tool condition.
Optical or laser scanning: these technologies allow for more detailed assessments of tool geometry, ensuring that each cutting edge is functioning properly.
The accuracy of these measurement techniques is critical in maintaining consistent cutting performance, particularly in mass production environments.
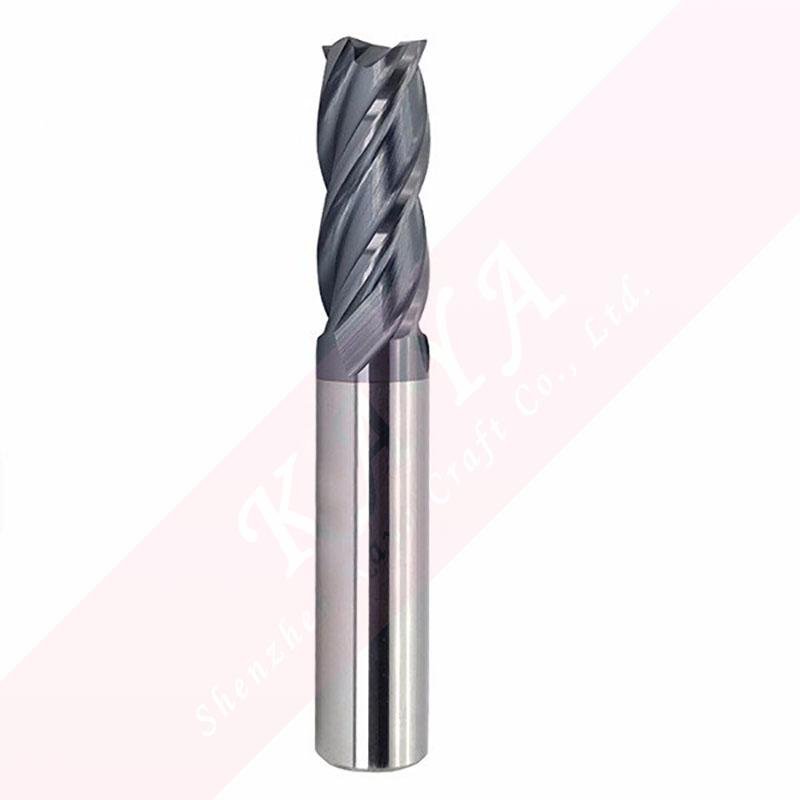
3. Impact of Cutting Edge Number on Milling Cutter Performance
Cutting Force and Cutting Efficiency
The number of cutting edges directly influences the cutting force and overall efficiency of the milling process. More cutting edges mean that the cutting load is distributed among multiple surfaces, which reduces the load on each individual edge. This leads to lower cutting forces, reducing the likelihood of tool deflection and vibration, and improving the efficiency of the machining process.
For example, a multi-edge cutter will allow for faster material removal compared to a single-edge cutter, as more material is engaged in each pass. This also improves chip removal and reduces the chances of material build-up on the cutting edges, which can otherwise hinder performance.
Cutting Torque and Tool Life
With more cutting edges, the cutting torque (the rotational force on the cutter) is spread out, reducing the overall load per edge. This results in lower wear per edge, increasing the tool's overall life. Multi-edge cutters are especially advantageous in heavy-duty applications where high cutting forces are generated, as they distribute the load evenly.
On the other hand, single-edge cutters experience higher wear rates on each cutting edge, leading to faster degradation and a shorter tool life. Therefore, multi-edge cutters are ideal for continuous and high-volume production processes.
Surface Finish Quality
The number of cutting edges also affects the surface quality of the workpiece. A multi-edge cutter often produces a better surface finish than a single-edge cutter due to the more frequent engagement of the cutting edges with the material. The smoother the cutting action, the less likely there will be tool marks or irregularities on the workpiece surface.
However, this also depends on the tool geometry and the machining conditions. Excessive cutting edges can sometimes cause problems like chatter or tool vibrations, leading to reduced surface quality.
4. Advantages and Disadvantages of Multi-Edge Cutters
Increasing Feed Rate and Machining Efficiency
One of the primary advantages of multi-edge cutters is their ability to increase the feed rate and overall machining efficiency. By engaging more cutting edges simultaneously, the cutter can remove more material in a given time, allowing for higher productivity. This makes multi-edge cutters ideal for mass production and high-speed machining operations.
Reducing Cutting Pressure on Single Edges
Multi-edge cutters reduce the cutting pressure on each individual edge, which minimizes tool wear and extends the tool's life. When the cutting pressure is spread across several edges, the forces on each edge are reduced, allowing the tool to perform efficiently for a longer period.
However, using multi-edge cutters comes with trade-offs. The complexity of manufacturing and balancing multi-edge tools can lead to higher initial costs, and in some cases, the increased number of edges can lead to issues such as chip evacuation problems or tool vibration.
5. Factors Influencing the Selection of Cutting Edge Number
Material Type and Hardness
The material being machined is one of the most important factors in choosing the number of cutting edges. Harder materials require more cutting edges to distribute the cutting forces evenly. Multi-edge cutters are generally preferred for softer materials like aluminum, brass, or plastics, where high-speed, high-efficiency machining is beneficial.
For harder materials like steel or titanium, while multi-edge cutters are still used, the tool must be designed to withstand the higher forces generated during cutting. In these cases, the geometry of the cutting edges (such as rake angle, clearance angle, and cutting edge radius) is also critical.
Machining Precision Requirements
The required precision of the machining process will also dictate the number of cutting edges. Multi-edge cutters typically provide better surface finishes and higher precision due to the increased frequency of engagement with the workpiece. However, if a very fine surface finish or tight tolerances are needed, single or double-edge cutters may be used in specialized finishing operations.
Machine Tool Performance and Tool Rigidity
The machine tool’s capabilities and the tool’s rigidity also influence the choice of cutting edge number. Machines with higher rigidity can handle multi-edge tools more effectively, maintaining better stability and cutting precision. On less rigid machines, using a multi-edge cutter may lead to vibrations or decreased cutting stability, especially at high speeds.
6. Application Analysis for Different Numbers of Cutting Edges
Single-edge cutters are used primarily for specialized tasks like engraving or operations requiring extremely high precision, where only one edge is needed for the specific application.
Double-edge cutters are suitable for general-purpose milling operations, including both roughing and finishing processes. They provide a good balance between tool strength and surface finish.
Multi-edge cutters are preferred in high-volume and high-speed machining, especially for soft materials or where high material removal rates are required. These cutters are commonly used in the automotive, aerospace, and mold-making industries, where speed and efficiency are essential.
The number of cutting edges in a milling cutter plays a critical role in determining the cutter’s performance and suitability for various applications. A higher number of cutting edges can enhance machining efficiency, tool life, and surface finish, making multi-edge cutters ideal for high-speed, high-volume operations. However, selecting the right cutter requires considering the material, required precision, and machine capabilities to ensure optimal performance. With the continued advancement in tool design and technology, manufacturers can now select from a wide range of cutting-edge configurations tailored to meet specific machining needs.
OEM Capability

Categories
HSS-PM Taps | HSSE-M42 Taps |
HSSE / HSS Taps | Spiral Flute Taps |
Straight Flute Taps | Spiral Point Taps |
Multi-function Taps |
Solid Carbide Drill Bits | Twist Drill Bits |
Center Drill Bits | Indexable U Drills |
Flat-end Milling Cutter | Ball Nose End Mills |